
Higher production costs, demand for quality textiles, and environmental legislation present challenges for the textile industry. “Novozymes’ solutions can contribute to decreasing dependence in the textile industry on chemicals, lower consumption of energy and water, and bring down costs – all while maintaining superior product quality,” says Sebastian Søderberg, Business Development & Marketing Director - Textile & Leather at Novozymes.
More savings and less use of valuable resources
Water is an increasingly scarce resource. Novozymes estimates that the global knitwear production uses the same amount of water as 24 million rural Chinese people use for drinking water. Fortunately, there are ways that the textile industry can consume less – and keep it cleaner. Enzymes can combine processes to save water usage, and they can also decrease the toxicity of effluents. Enzymes also necessitate fewer rinses after one process as compared to chemicals.
Novozymes solutions can reduce water and energy usage to a great extent simply by being applied at different stages of the same textile production process. Esquel Group, a leading producer of cotton shirts and a global textile and apparel manufacturer, has performed several trials applying Novozymes’ bioinnovative solutions at the different stages of the production.
According to a Live Cycle Assessment conducted by Novozymes, Esquel Group achieved a saving of 30 cubic meters of water per ton of knitted fabric in just one single process (bleaching) by using Novozymes enzymatic solution as compared to using conventional technology.
Read more on Towards a better and cleaner textile industry @ Fibre2fashion
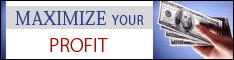
No comments:
Post a Comment